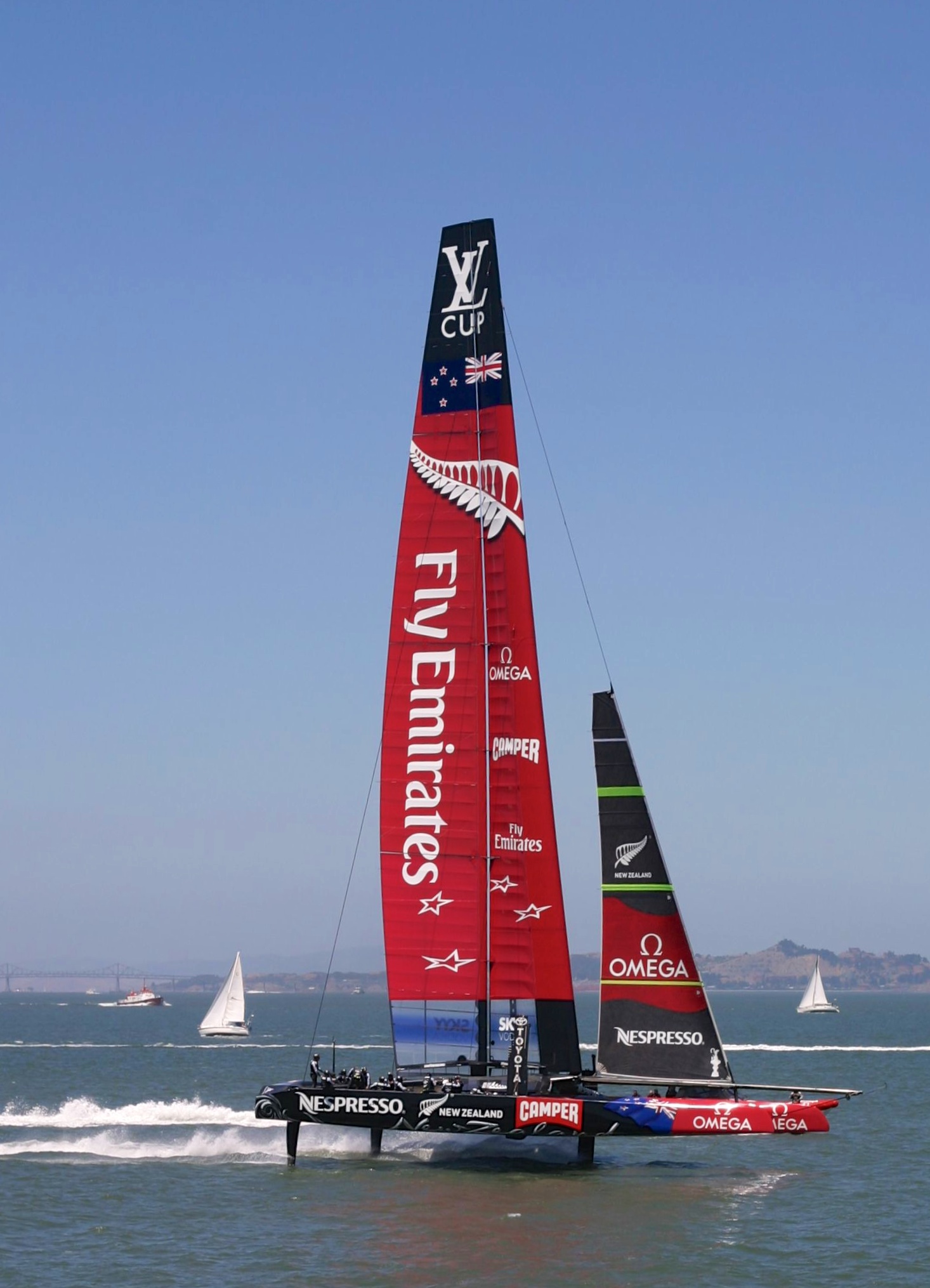
Mechanical Engineering
For the first time, the America's Cup was sailed with foiling boats in 2013. This led to fast growth in the use of foils on sailing and power boats, both for racing and cruising. Foiling allows unprecedented speed and comfort, but it raises significant design challenges regarding control and safety. In the recent 2024 America's Cup, boat speeds over 50 knots have been reached.
The project aims to develop an in-depth understanding of the unsteady hydrodynamics of America's Cup hydrofoils, including issues related to cavitation and ventilation. It will be performed in partnership with world-leading yacht designers and professional sailors and potentially affiliated with an America Cup team.
There is no closing date for this position, which will remain open until filled.
Prof. Viola leads the Vortex Interaction Laboratory, VOILAb (https://voilab.eng.ed.ac.uk)
Minimum entry qualification - an Honours degree at 2:1 or above (or International equivalent) in a relevant science or engineering discipline, possibly supported by an MSc Degree. Further information on English language requirements for EU/Overseas applicants.
Applications are welcomed from those who have secured their own funding through scholarships or sponsorships. No internal funds are available for this project.
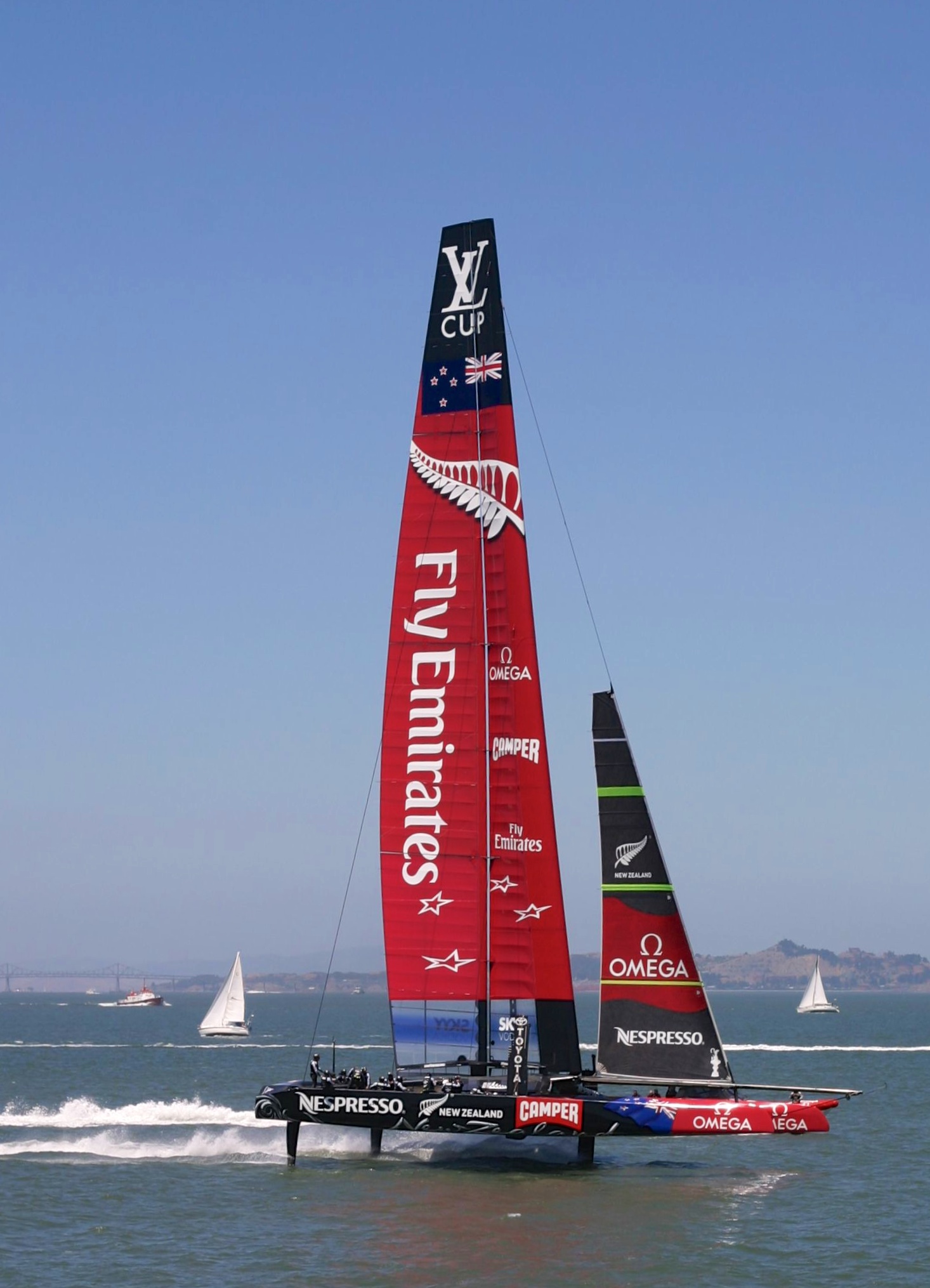
The Javan cucumber (Alsomitra macrocarpa) is a vine that climbs the trees of tropical forests toward the canopy and sunlight. At great heights, it grows pods that contain hundreds of winged seeds. As the wind blows against the opening of the pods, the samaras are peeled away and released. Unlike many gliding seeds that use auto-rotation, the seed of the Javan cucumber vine exhibits a stable gliding flight with its paper-thin wings. The seed's design is efficient enough to achieve a slower rate of descent compared to that of rotating winged seeds. This aerodynamic advantage allows the seed to be easily carried by the wind several hundred metres. It is possible for the seeds to glide up to hundreds of meters, ensuring that they spread far from each other as well as the parent pod. This wide dispersal prevents the seeds from competing for resources once they fall to the ground and begin growing.
The membranous wings of the Alsomitra macrocarpa fruit are very thin, varying from a few micron to some tens of microns. The wing has a swept and tapered planform, resembling that of a flying wing (see figure). Such a wing is one of the most efficient fixed-wing aircraft designs, since the entire body provides lift; however, without electronic stablisers, “flying wing” aircraft are difficult to control. The Alsomitra macrocarpa fruit, however, has overcome this design weakness by having a center of gravity located close to (but in front of) the aerodynamic center of the wing due to the swept planform. At the same time, elastic deformation of the wing provides a twisted washout and dihedral, which helps it fly in a straight path and prevents “spiral instability” [1].
This project aims to reveal the origin of this fruit's incredible flight capacity. We will achieve this through numerical modelling of the wing using computational fluid dynamics, and flow visualisation and particle image velocimetry techniques with real seeds and scaled-up models of the seeds.
There is no closing date for this position, which will remain open until filled.
[1] Azuma, A., 2012. The biokinetics of flying and swimming. Springer Science & Business Media.
Prof. Viola leads the Vortex Interaction Laboratory, VOILAb (https://voilab.eng.ed.ac.uk)
Minimum entry qualification - an Honours degree at 2:1 or above (or International equivalent) in a relevant science or engineering discipline, possibly supported by an MSc Degree. Further information on English language requirements for EU/Overseas applicants.
Applications are welcomed from those who have secured their own funding through scholarships or sponsorships. No internal funds are available for this project.
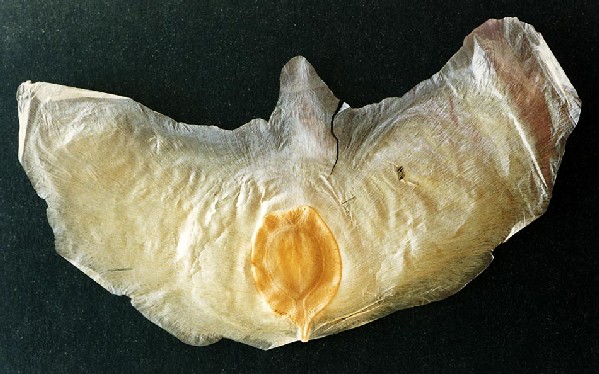
The proposed project aims to investigate the fluid dynamics of yacht sails. Sails have unique flow features, which allow the generation of very high lift and high lift/drag ratio compared to wings and blades commonly used in other fields such as aeronautics and turbomachinery. The project aims to understand the underlying mechanisms of these flow features in order to further enhance the performance of sails and, importantly, to allow the cross-fertilisation of ideas in research fields where there is a need for fluid dynamic efficiency.
The flow field around sails has several uncommon characteristics. The sharp leading edge leads to laminar separation, followed by a laminar-to-turbulent transition and then turbulent reattachment, forming a leading edge vortex (LEV). LEVs are known on flat plates with a sharp leading edge and on delta wings, while on rounded-nose foils used for low-pressure turbines, a similar feature known as the laminar separation bubble (LSB) occurs.
In the present project, it is proposed to test large-scale flexible sails in a wind tunnel to measure forces and the flying shape of sails and then to build a rigid small-scale model to be tested in a water tunnel to perform flow measurements with particle image velocimetry. Experimental measurements will be complemented with computational fluid dynamics simulations to test a wide range of conditions, which are tested with difficulty experimentally.
There is no closing date for this position, which will remain open until filled.
Prof. Viola leads the Vortex Interaction Laboratory, VOILAb (https://voilab.eng.ed.ac.uk)
Minimum entry qualification - an Honours degree at 2:1 or above (or International equivalent) in a relevant science or engineering discipline, possibly supported by an MSc Degree. Further information on English language requirements for EU/Overseas applicants.
Applications are welcomed from those who have secured their own funding through scholarships or sponsorships. No internal funds are available for this project.
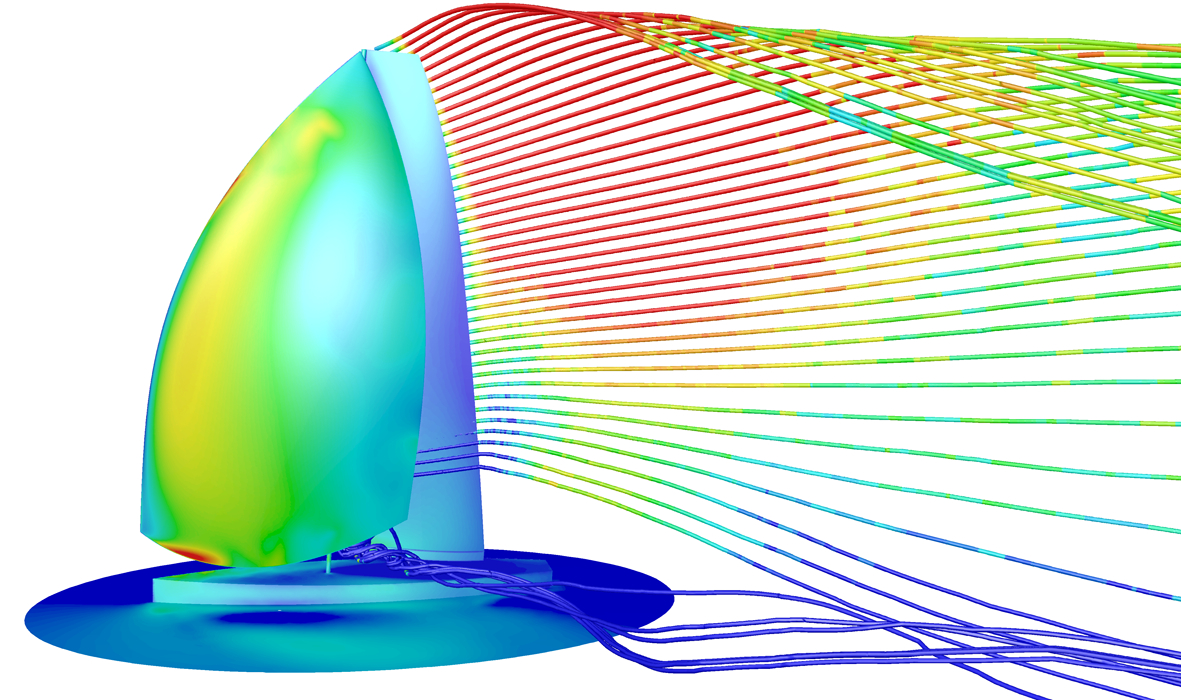
This project aims to investigate the capabilities of adaptive structures that change their geometry and mechanical properties to accommodate operational loading and extend their lifespan, thereby supporting sustainable infrastructure and a circular economy.
The core objective of this project is to engineer a self-adapting structure that adjusts to the prescribed loading conditions. This adaptation is achieved by integrating local structures that accommodate stiffness variations along the global structure. The local structures will change their geometry and shape in response to the applied loads, resulting in emergent properties in the main global structure. Analytical modeling of the sub-structures will provide understanding and control for stiffness tailoring, which will translate into desirable mechanical properties in the main structure. The connection between global properties and sub-structure geometry changes aims to be achieved by understanding the relationships between geometric parameters and vibration response. The geometric nonlinearity induced by the local sub-structures may cause amplitude-dependent nonlinear dynamic responses. Thus, understanding the underlying physics in the coupling between local and global structures, along with the vibration response of the global structure, aims to facilitate feedback to passively control the mechanical properties of the structure. Consequently, this dynamic response leads to continuous shape and geometry modifications within the structure, ultimately enhancing its capacity to accommodate specified loading requirements more effectively. The adaptive structures will benefit operability by maximizing structural capacity during service.
This project is supervised by Dr David Garcia Cava (School of Engineering, University of Edinburgh). It will involve regular interaction with collaborators from academia and industry. Interested candidates may contact the supervisor for further information (david.garcia@ed.ac.uk).
Personal website: https://dgarciacava.github.io/
This advert might close once a suitable candidate is found. Please apply as soon as possible to avoid disappointment.
References
[1] Sundararaman, V., O’Donnell, M.P., Chenchiah, I.V., Clancy, G. and Weaver, P.M., 2023. Stiffness tailoring in sinusoidal lattice structures through passive topology morphing using contact connections. Materials & Design, 226, p.111649.
[2] Zhao, B., Thomsen, H.R., Pu, X., Fang, S., Lai, Z., Van Damme, B., Bergamini, A., Chatzi, E. and Colombi, A., 2024. A nonlinear damped metamaterial: Wideband attenuation with nonlinear bandgap and modal dissipation. Mechanical Systems and Signal Processing, 208, p.111079.
The University of Edinburgh is committed to equality of opportunity for all its staff and students, and promotes a culture of inclusivity. Please see details here: https://www.ed.ac.uk/equality-diversity
Minimum entry qualification - an Honours degree at 2:1 or above (or International equivalent) in a relevant science or engineering discipline, possibly supported by an MSc Degree.
Applications are particularly welcome from candidates expecting to receive a first-class degree in mechanical engineering, physics, applied mathematics or a closely related subject.
Interests on: Structural mechanics and dynamics, Stochastic modelling and uncertainty quantification.
Further information on English language requirements for EU/Overseas applicants.
Applications are welcomed from self-funded students, or students who are applying for scholarships from the University of Edinburgh or elsewhere.
*Competition (EPSRC) funding may be available for an exceptional candidate but please note you must be a UK student or an EU student who has pre-settled/settled status and has lived in the UK for at leats 3 years.
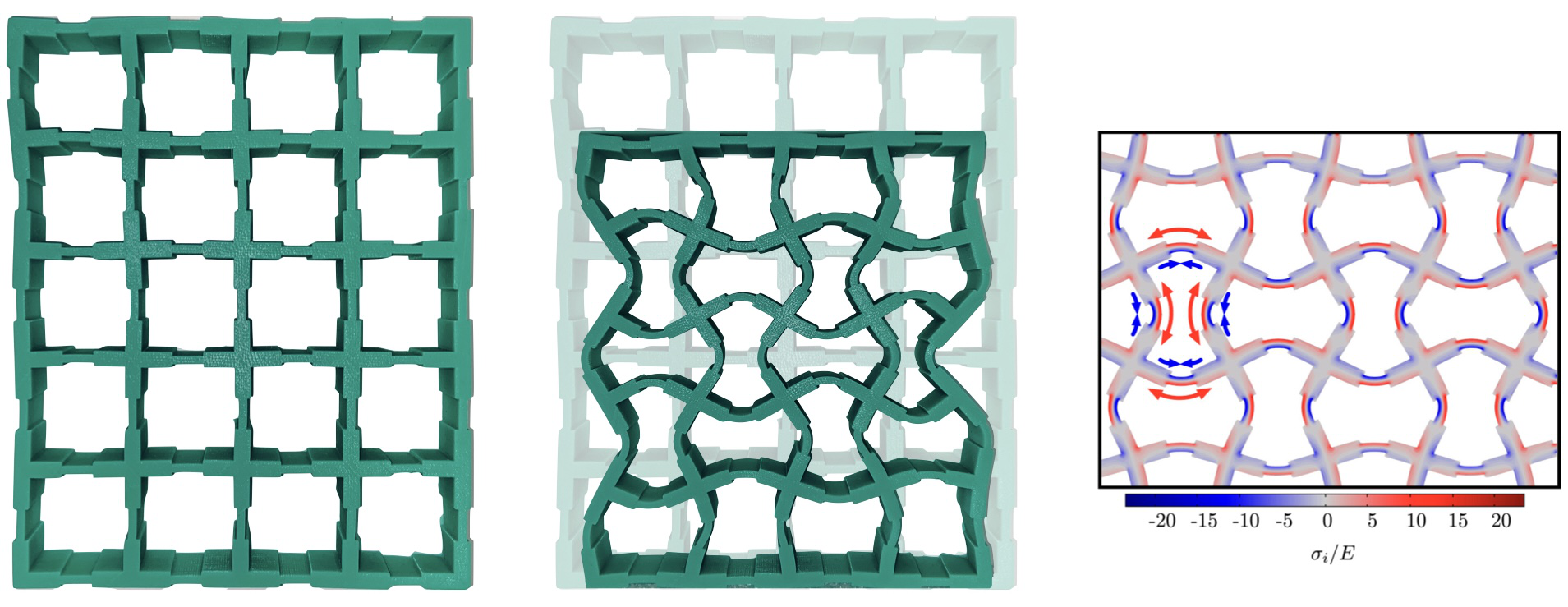
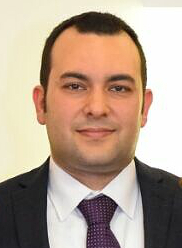
I am a Lecturer in Mechanical Engineering at the Institute for Materials and Processes in Edinburgh University. My expertise is in the modeling and simulation of particle (granular)/particle-laden systems. These systems are encountered in a broad spectrum of industrial and environmental applications ranging from manufacturing to aerospace industries. To study the multi-physics and multi-scale phenomena encountered in such systems, I develop bespoke parallel numerical schemes and use high-performance computing to discover new physics and to tackle challenging engineering issues.
- BSc, MSc, PhD
- PgDip In Academic Practice
- Member of the Institution of Mechanical Engineers (MIMechE)
- Fellow of Advance HE (FHEA)
- Engineering Thermodynamics (SCEE08006)
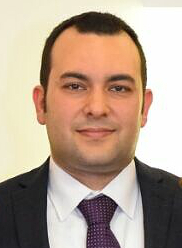
I am a Lecturer in Mechanical Engineering at the Institute for Materials and Processes in Edinburgh University. My expertise is in the modeling and simulation of particle (granular)/particle-laden systems. These systems are encountered in a broad spectrum of industrial and environmental applications ranging from manufacturing to aerospace industries. To study the multi-physics and multi-scale phenomena encountered in such systems, I develop bespoke parallel numerical schemes and use high-performance computing to discover new physics and to tackle challenging engineering issues.
- BSc, MSc, PhD
- PgDip In Academic Practice
- Member of the Institution of Mechanical Engineers (MIMechE)
- Fellow of Advance HE (FHEA)
- Engineering Thermodynamics (SCEE08006)
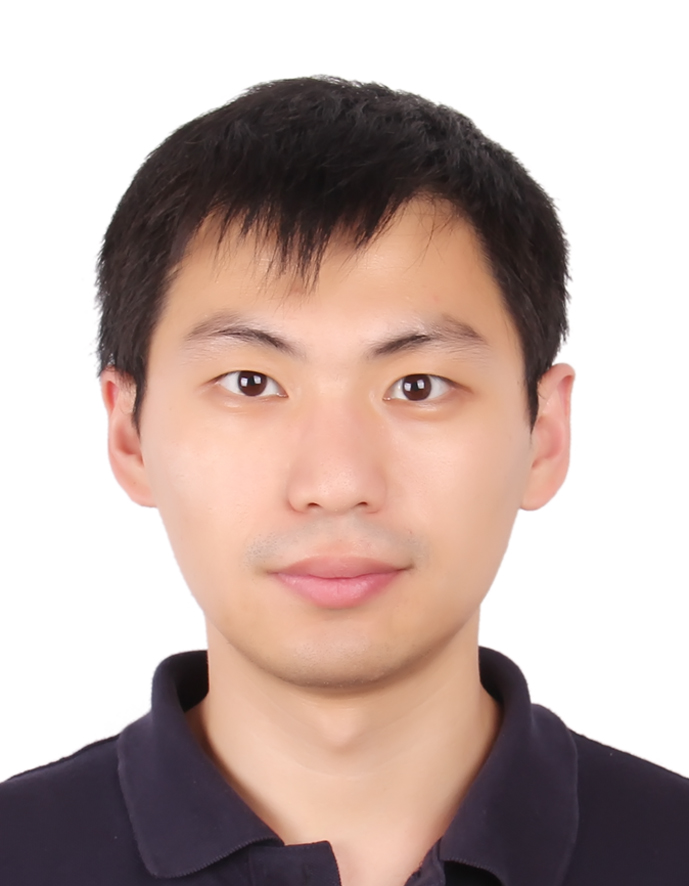
Dr Nan Yu is a Senior Lecturer/Associate Professor at the University of Edinburgh, and the Deputy Director of MSc Digital Design and Manufacture.
Nan was trained at Cranfield University (PhD: plasma figuring of large optics), University College Dublin (UCD, as a postdoc in precision manufacturing of medical devices), and the European Organisation of Nuclear Research (CERN, as an Associate Scientist in precision alignment and metrology). He has established academic reputation in precision manufacturing and advanced plasma technologies as evidenced by over £ 1 M funding secured as PI, more than 50 papers in peer-reviewed journals and conferences, 4 paper awards and 10 invited/keynote talks. Nan receives the prestigious Marie Curie International Fellowship (2018-2020), Irish Research Council Fellowship (2020), and Royal Academy of Engineering Industrial Fellowship (2023-2024). He holds two visiting appointments at UCD (2021-2026) and Osaka University (2022-2024).
PgCAP in Higher Education (2023), Edinburgh
PhD in Precision Engineering (2017), Cranfield
MSc in Mechanical Manufacturing (2013), Harbin;
BSc in Mechanical Engineering (2011), Harbin;
2018 Professional Certificate of Entrepreneurial Educators, UCD, National University of Ireland;
2018 International Scientific Committee member of European Society for Precision Engineering and Nanotechnology (EUSPEN);
2019 Member of International Academy of Engineering and Technology (AET);
2021 Research Affiliate of International Academy of Production Engineering (CIRP);
2021 Member of EPSRC Early Career Forum in Manufacturing Research;
2022 Fellow of Royal Society for Art, Manufacture and Commerce (RSA);
2023 Fellow of Higher Education Academy (HEA)
1. Conceptual Design for Mechanical Engineers 3 (Course Organiser);
2. BEng Mechanical Engineering Project 4;
3. Digital Manufacturing 5;
4. Metrology in MSc Digital Design and Manufacture (Course Organiser)
5. MEng Mechanical Engineering Project 5
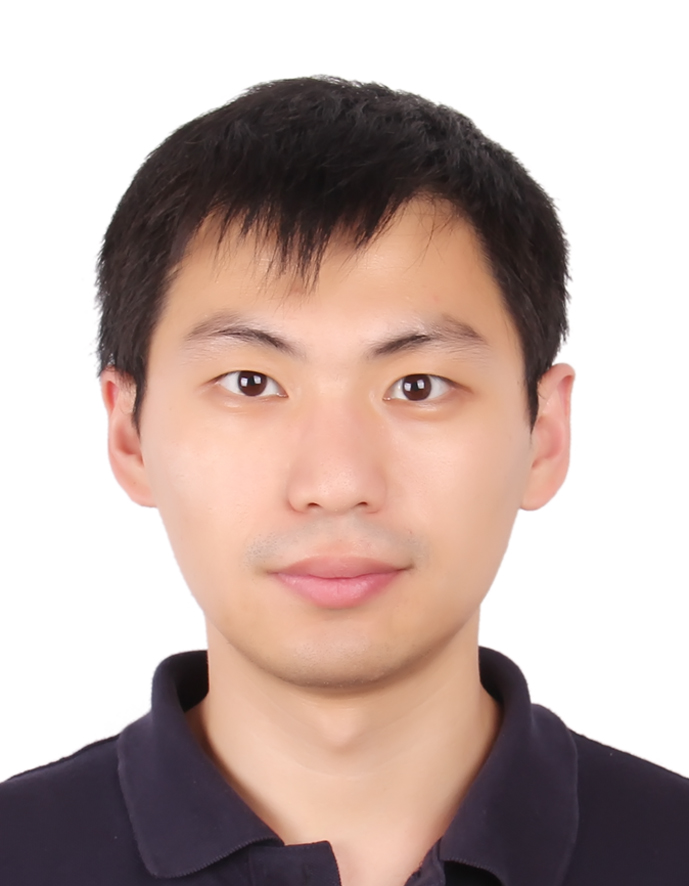
Dr Nan Yu is a Senior Lecturer/Associate Professor at the University of Edinburgh, and the Deputy Director of MSc Digital Design and Manufacture.
Nan was trained at Cranfield University (PhD: plasma figuring of large optics), University College Dublin (UCD, as a postdoc in precision manufacturing of medical devices), and the European Organisation of Nuclear Research (CERN, as an Associate Scientist in precision alignment and metrology). He has established academic reputation in precision manufacturing and advanced plasma technologies as evidenced by over £ 1 M funding secured as PI, more than 50 papers in peer-reviewed journals and conferences, 4 paper awards and 10 invited/keynote talks. Nan receives the prestigious Marie Curie International Fellowship (2018-2020), Irish Research Council Fellowship (2020), and Royal Academy of Engineering Industrial Fellowship (2023-2024). He holds two visiting appointments at UCD (2021-2026) and Osaka University (2022-2024).
PgCAP in Higher Education (2023), Edinburgh
PhD in Precision Engineering (2017), Cranfield
MSc in Mechanical Manufacturing (2013), Harbin;
BSc in Mechanical Engineering (2011), Harbin;
2018 Professional Certificate of Entrepreneurial Educators, UCD, National University of Ireland;
2018 International Scientific Committee member of European Society for Precision Engineering and Nanotechnology (EUSPEN);
2019 Member of International Academy of Engineering and Technology (AET);
2021 Research Affiliate of International Academy of Production Engineering (CIRP);
2021 Member of EPSRC Early Career Forum in Manufacturing Research;
2022 Fellow of Royal Society for Art, Manufacture and Commerce (RSA);
2023 Fellow of Higher Education Academy (HEA)
1. Conceptual Design for Mechanical Engineers 3 (Course Organiser);
2. BEng Mechanical Engineering Project 4;
3. Digital Manufacturing 5;
4. Metrology in MSc Digital Design and Manufacture (Course Organiser)
5. MEng Mechanical Engineering Project 5
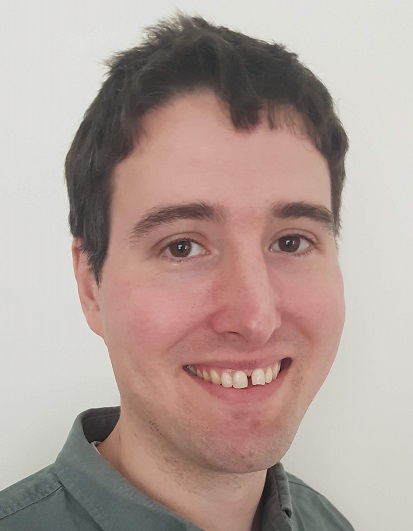
- MEng, Aerospace Engineering, The University of Manchester, 2010
- PhD, Advanced Metallic Systems, The University of Manchester, 2015
- PGCert, Academic Practice, LJMU, 2021
- Fellow of Advance HE (FHEA)
- Member of The Institute of Materials, Minerals & Mining (MIMMM)
Sam is currently course organiser for three courses:
- Additive and Computer Aided Manufacturing (PGEE11210)
- Digital Design and Manufacture Dissertation (PGEE11217).
- Digital Manufacture 5 (MECE11017)
He also provides supervision for BEng, MEng and MSc projects.
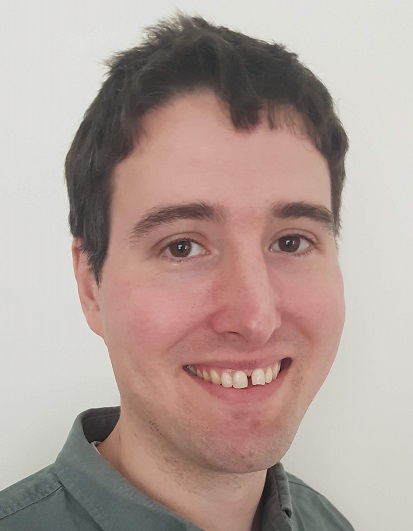
- MEng, Aerospace Engineering, The University of Manchester, 2010
- PhD, Advanced Metallic Systems, The University of Manchester, 2015
- PGCert, Academic Practice, LJMU, 2021
- Fellow of Advance HE (FHEA)
- Member of The Institute of Materials, Minerals & Mining (MIMMM)
Sam is currently course organiser for three courses:
- Additive and Computer Aided Manufacturing (PGEE11210)
- Digital Design and Manufacture Dissertation (PGEE11217).
- Digital Manufacture 5 (MECE11017)
He also provides supervision for BEng, MEng and MSc projects.